Proces produkcji pamięci komputerowych RAM marki Goodram
I. Proces montażu
Montaż SMT przebiega na jednej z najnowocześniejszych linii montażowych w Europie. Wykorzystywane są do tego maszyny firmy Panasonic, które stanowią o najwyższym poziomie jakości montażu przy zachowaniu bardzo wysokiej wydajności.
Przed rozpoczęciem produkcji, oprócz zamówienia elementów elektronicznych, konieczne jest zamówienie szablonu do drukarki szablonowej. Ze względu na wymaganą wysoką precyzję nadruku pasty lutowniczej, szablony wykonuje się z blachy ze stali nierdzewnej o dobranej do produktu grubości, która wycinana jest laserowo. W niektórych przypadkach stosuje się dodatkowo elektropolerowanie, co pozwala na uzyskanie dodatkowych właściwości w trakcie czynności nadruku pasty.
Przygotowane w ten sposób sita są dostosowywane do standardu systemu VectorGuard, który wykorzystywany jest w firmie. Do wykonania każdego sita konieczne jest odpowiednie przygotowanie danych technicznych, takie jak przeliczenie objętości pasty nanoszonej poprzez sito, zdefiniowanie kształtu bryły pasty po nadruku, ewentualne zastosowanie redukcji apertury lub tzw. „overprintu”.
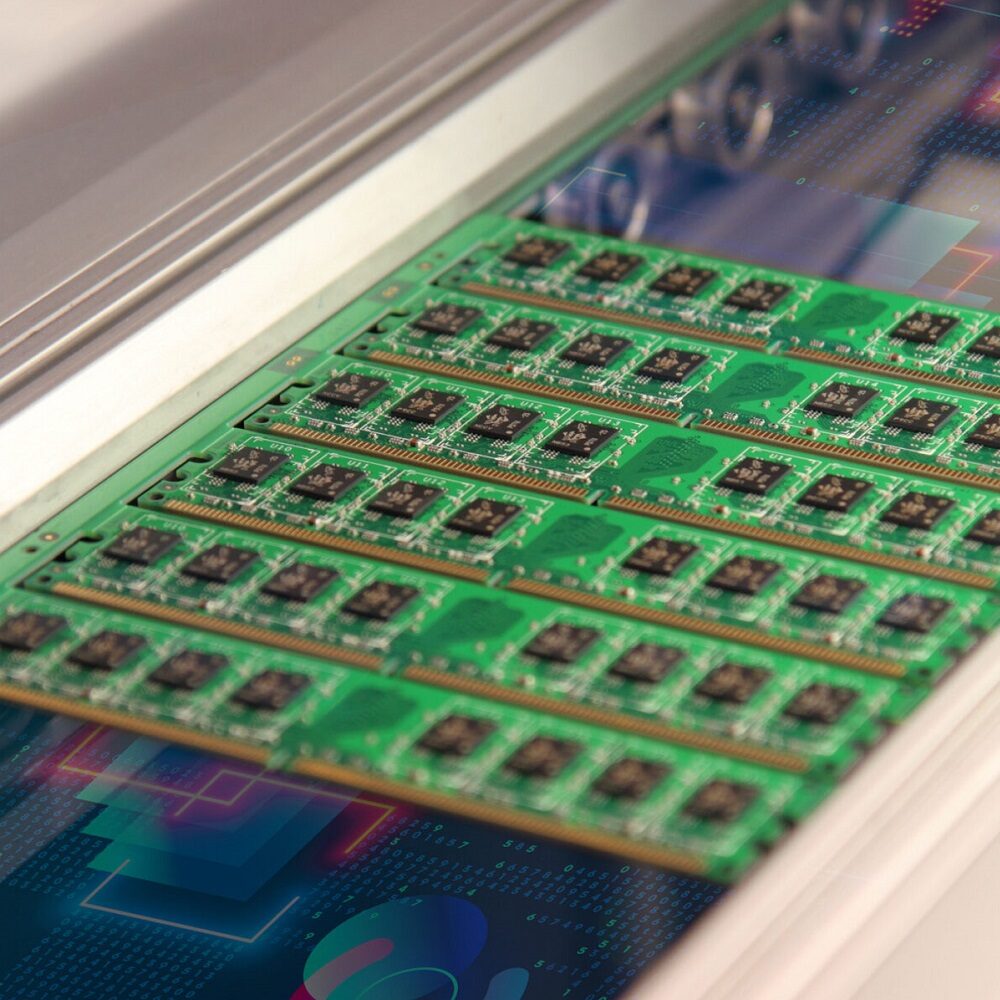
- Pierwszym etapem montażu jest nadruk pasty lutowniczej realizowany przez drukarkę szablonową (sitodrukarkę) Panasonic SPG. Jej zadaniem jest precyzyjne naniesienie pasty lutowniczej na płytkę drukowaną poprzez specjalnie przygotowany, dedykowany do produktu szablon. Od precyzji nadruku zależy, czy wyrób końcowy z linii SMT będzie poprawnie wyprodukowany i nie będzie posiadał wad takich jak np. zwarcia pomiędzy wyprowadzeniami komponentów.
- Płytka drukowana z naniesioną pastą jest transportowana automatycznie do maszyny SPI z ang. „Solder paste inspection” PARMI SIGMA-X, gdzie poddawane są kontroli w procesie automatycznej inspekcji, wykorzystującej do tego precyzyjne lasery. Inspekcja trwa kilka sekund, a maszyna sprawdza precyzyjność i poprawność nałożenia pasty lutowniczej na PCB, ta, po weryfikacji zostaje przekazywana do montażu elementów pasywnych.
- Montaż elementów pasywnych odbywa się w maszynach Panasonic NPM-D2 odpowiadających za montaż elektronicznych komponentów SMD – zarówno pasywnych, jak i aktywnych. Maszyny NPM-D2 oferują bardzo wysoką wydajność przy jednoczesnym zastosowaniu bardzo zaawansowanych metod kontroli komponentów SMD przed montażem na płytce PCB. W trakcie montażu komponentów pasywnych sprawdzane są parametry takie jak m.in. długość, szerokość i wysokość komponentu, a dla komponentów z wyprowadzeniami w postaci nóżek lub kulek sprawdzana jest dodatkowo liczba wyprowadzeń, ich rozmiar, ewentualne odchyłki wymiarowe itp. Do weryfikacji tych parametrów używane są kamery 2D i 3D, które przeprowadzają kontrolę w ciągu ułamku sekundy dla wszystkich komponentów przenoszonych przez głowicę montażową.
- Maszyny Panasonic NPM-D2 posiadają nowoczesną budowę modularną, co pozwala na zwiększenie wydajności poprzez dostawianie kolejnych modułów do linii produkcyjnej.
- Do obsługi linii produkcyjnej dedykowane jest specjalne oprogramowanie Panasonic DGS, w którym przygotowuje się programy zgodnie z BOM (struktura materiałowa wyrobu), definiuje parametry komponentów, zbiera informacje o wydajności oraz jakości procesu.
- Po zmontowaniu całego pakietu trafia on na stanowisko kontroli wizualnej, gdzie wyszkolony operator sprawdza poprawność montażu powierzchniowego.
- Następnym etapem jest lutowanie w piecu rozpływowym. Piec rozpływowy ma za zadanie podgrzanie pakietu do temperatury lutowania, a następnie wychłodzenie do temperatury otoczenia. Aby połączenia lutownicze posiadały odpowiednie właściwości i były pozbawione wad, wymagane jest precyzyjne ustawienie krzywej temperaturowej (profilu) i rygorystyczne pilnowanie tych parametrów. Profil grzewczy uzyskuje się poprzez zestawienie rekomendowanych przez dostawcę pasty parametrów procesowych z parametrami wynikającymi z charakterystyki pakietu (rodzaj zastosowanych komponentów SMD) oraz wymaganym cyklem pracy. Tak przygotowany wstępny profil poddawany jest testom z użyciem komponentów elektronicznych oraz specjalnego urządzenia kontrolno-pomiarowego – ECD SuperM.O.L.E Gold 2. W przypadku zróżnicowanych pakietów elektroniki, ustawienie odpowiedniego profilu wymaga dużej wiedzy i doświadczenia pracownika. Jakość lutowia kontrolowana jest pod mikroskopem i w maszynie do kontroli rentgenowskiej.
- Kolejnym etapem produkcji jest kontrola z użyciem maszyny AOI z ang. „Automated Optical Inspection”. Panele za pośrednictwem bardzo wydajnych maszyn AOI PARMI Xceed są poddane zautomatyzowanej kontroli wykorzystującej laser, maszyna sprawdza poprawność lutowania i jakość spoin, a także sprawdzana jest wysokość ułożenia komponentów pasywnych, weryfikowane są uszkodzenia mechaniczne soldermaski PCB.
- Dla wyrobu produkowanego przy użyciu układów BGA (Ball Grid Array) przewidziana jest dodatkowa kontrola w procesie, mająca na celu sprawdzenie poprawności połączeń. Układy BGA posiadają wyprowadzenia pod układem, które po procesie lutowania są niewidoczne gołym okiem, wobec czego wymagane jest użycie maszyny rentgenowskiej. Zastosowana w WESA maszyna generuje promieniowanie za pomocą odpowiedniej aparatury zasilanej prądem elektrycznym, dzięki czemu zapewniona jest pełna kontrola nad czasem trwania oraz mocą promieniowania. Na podstawie uzyskanych zdjęć wyszkolony personel jest w stanie określić, w którym miejscu linii SMT wystąpiły ewentualne problemy i jak im zapobiec.

II. METODOLOGIA TESTOWANIA MODUŁÓW PAMIĘCI DRAM
- Pierwszym etapem kontroli modułów pamięci DRAM po procesie montażu SMT jest test OPEN/SHORT, podczas którego sprawdzana jest poprawność montażu, a do modułów wgrywana jest ich konfiguracja. Test jest wykonywany przy pomocy specjalizowanych testerów wyprodukowanych przez CST – jednego z zaledwie kilku producentów tego typu urządzeń na świecie. Te zaawansowane urządzenia w krytycznych sytuacjach pozwalają na dokonanie pomiarów elektrycznych modułów pamięci i wyeliminowanie błędów z procesu.
- Moduły pamięci DRAM, które pozytywnie przeszły pierwszy etap kwalifikacji, zostają poddane kolejnemu testowi zwanemu testem aplikacyjnym, w którym stosowany jest autorski program testowy Wilk Elektronik. Tak jak typowy system operacyjny, program do testowania zarządza pamięcią oraz zadaniami, w ramach których odbywa się proces zapisu/odczytu oraz weryfikacja danych wzorcowych. Te zbudowane są w ten sposób, by symulować intensywną pracę modułów w komputerze taką jak przetwarzanie obrazu lub dźwięku bądź pracę aplikacji wielowątkowych. W sytuacji, gdy program wykryje przekłamanie danych wzorcowych, sygnalizowany jest błąd. Dzięki specjalnie zbudowanym w Wilk Elektronik algorytmom, program umożliwia zlokalizowanie uszkodzonego układu pamięci. Należy podkreślić, że budowa algorytmów testowych wymaga aktualizacji tak, aby zapewnić maksymalną skuteczność diagnostyczną dla każdych nowych układów pamięci wprowadzanych do procesu produkcji. Podobnie rozbudowa stanowisk testowych o nowe modele płyt głównych PC wymaga aktualizacji programu testowego w celu dodania nowych algorytmów wskazujących lokalizację uszkodzenia. Algorytmy te są tworzone unikalną metodą wypracowaną w Wilk Elektronik. Zmiany i aktualizacje oprogramowania są opracowywane i wdrażane przez dział Laboratorium Wilk Elektronik.
- Działanie programu testującego jest kontrolowane poprzez sieć LAN. Program pobiera z serwera ustawienia testu i porównuje z testowanym modułem pamięci. Jeżeli np. szybkość lub pojemność pamięci są różne od zadanych poprzez konfigurację stanowiska testowego, sygnalizowany jest błąd. Jest to dodatkowy etap kontroli potwierdzający poprawność wgranej konfiguracji. Na tym etapie program zapisuje w logach serwera wynik testu, gdy wskazuje on uszkodzenie, również z zapisaniem listy testów, które wykryły uszkodzenie. W ten sposób tworzona jest statystyka pozwalająca na doskonalenie procedur testowych i podnoszenie jakości produkowanych przez Wilk Elektronik pamięci. Z procesem podnoszenia jakości wiążą się procedury postępowania, według których w cyklu kwartalnym analizowana jest statystyka reklamacji oraz aktualizowany jest katalog procedur testowych. Zatem w procesie realizowany jest cykl Deminga, w którym znajduje się planowanie, wdrażanie, sprawdzanie, poprawianie procedur testowych.
- Identyfikacja produktów jest zapewniona poprzez unikalny numer testu zapisany przez program testujący w pamięci EEPROM oraz numer seryjny na etykiecie. Dzięki temu możliwe jest powiązanie modułu pamięci z informacjami o przebiegu procesu testowania oraz zleceniem produkcyjnym, a dalej z BOM oraz dostawcami. Nadrzędnym celem tej procedury jest zapewnienie identyfikowalności produktów wymaganej przez szerokie grono kontrahentów.
- Ostatnim etapem przyjętej przez Wilk Elektronik metodologii testowania jest ocena wyników otrzymanych z procesu testowania. Odbywa się to w dziale kontroli jakości, który decyduje o odpuszczeniu produktu do sprzedaży. W tym zakresie pomoc stanowi katalog procedur testowych, w którym zdefiniowane są progi odpadu tzw. „progi re-testu”, po przekroczeniu których następuje ponowienie procedury testowej. Ten sposób postępowania wiąże się z tzw. „krzywą wannową”, według której uszkodzenia powstające w pierwszym okresie użytkowania mogą być pobudzane za pomocą testów w aplikacji. Podążając za definicją krzywej, malejący odpad w kolejnych powtarzanych cyklach testu wskazuje na osiągnięcie przez produkt okresu „życia”, w którym uszkodzenia powinny powstawać jedynie w skutek niewłaściwej eksploatacji lub uszkodzenia mające charakter losowy.
- Uzupełnieniem możliwości diagnostycznych pamięci na stanowiskach testowych jest ich walidacja w komorze klimatycznej. Walidacja w komorze pozwala na potwierdzenie prawidłowego projektu oraz budowy pamięci, doboru komponentów, procesu montażu i zapewnia potwierdzenie możliwości pracy w wyspecyfikowanych parametrach. Walidacja w komorze klimatycznej przebiega zgodnie ze specyfikacją klienta lub ogólnoświatowym standardem z rodziny IEC60068. Walidacja w komorze termicznej może się odbywać w temperaturze od -70ºC aż do 180ºC oraz wilgotności do 95% przy 95ºC. Co więcej, metody uszczelnienia komory klimatycznej tj. zabezpieczenie przed przenikaniem wilgoci, zostały opracowane na potrzeby procesu przez Wilk Elektronik. Proces walidacji dostosowywany jest do bieżących potrzeb klientów tj. wymaga on procedur przygotowania urządzeń oraz przebiegu procesu. To samo tyczy się oprogramowania użytego w celu weryfikacji poprawności pracy w warunkach klimatycznych. Przyjęte w Wilk Elektronik procedury pozwalają na stosowanie sprzętu dostarczonego przez klienta.
III. Środowisko pracy
W celu zapewnienia odpowiednich warunków BHP, poprawnej pracy maszyn, wysokiej jakości wyrobu, w procesie produkcyjnym muszą być zachowane odpowiednie warunki, m.in.:
- Odpowiednia odzież dla pracowników typu:
- Obuwie ESD,
- Fartuch ESD,
- Rękawice ESD,
- Opaski nadgarstkowe ESD.
- Klimatyzacja hali w celu utrzymania stałej temperatury – prowadzony jest stały pomiar temperatury i wilgotności.
- Klimatyzacja miejscowa – zastosowanie dedykowanego klimatyzatora Panasonic do drukarki szablonowej Panasonic SPG utrzymującego wewnątrz maszyny stałe warunki pracy.
- Zapewnienie maksymalnej czystości – ograniczenie zanieczyszczeń i eliminacja kurzu.
- Utrzymanie maszyn i urządzeń w pełnej sprawności i czystości – zastosowano metodologię TPM w celu zapewnienia realizacji prac prewencyjnych.
- Zabezpieczenie przed ESD wraz z wyznaczonymi strefami EPA
- posadzka ESD,
- odzież ESD,
- uziemianie stanowisk,
- specjalne maty bądź blaty stanowisk roboczych,
- eliminowanie emiterów wyładowań ze stery EPA
- pomiary ochrony przed ESD przeprowadzane przez pracowników przed przystąpieniem do pracy,
- czyszczenie stanowisk dedykowanym płynem czyszczącym ESD.